Improving workplace health and safety performance in Australia
- Australia Industry Expert
- Dec 19, 2019
- 2 min read
Workplace safety risk management is a challenge that has the potential to impact a business regulatory compliance, internal policy management, brand, reputation and finances.
By merging decisive statistical methods and leveraging multiple contrasting data sources, businesses are able to understand the drivers of occupational accidents that were previously unseen. Organisations can then use these insights to more effectively address occupational safety in terms of both injury prevention and injury management.
Morshona has developed Projecting Safety Analytics, an approach which uses a range of refined analytics techniques, to provide greater understanding and clarity into health and safety systems, and to help its clients develop processes and design interventions to minimise such risk.
The approach can help your organisation answer some of the following important questions:
What metrics can provide the ability to take evidence-based safety focus on “proactive indicators” to craft more actionable insights, rather than the conventional simple reactive reporting of claims and incidents?
Which work processes or operational areas have the highest risk factors for incidents?
What would be the impact of proposed changes to training, teaming and scheduling?
Given the highly variable nature of accidents, what precautionary measures offer the best value across a range of future outcomes, when a safety program has financial restraints?
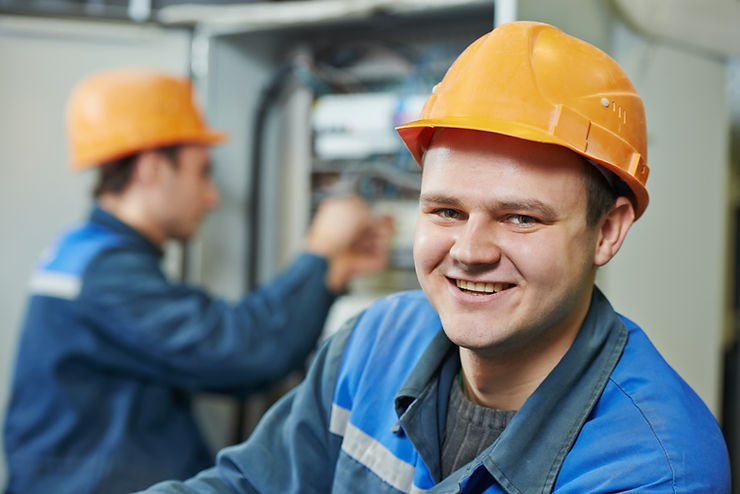
Preventative Safety Analytics
1. Organisation understanding
Understand project objectives and requirements from an organisation perspective.
This phase begins with an agreement on the health and safety challenge(s), the approach for incorporating the visions from the project into the organisation, defining the operating environment and determining the available assets and finally setting an “analytics plan” to achieve these outcomes.
2. Information understanding
Collect information and then become familiar with it (quality and initial insights).
The information extracts from the information assets are gathered. This normally includes: safety claims, incidents and observations, operational data, HR information, work site data, production data and other external data sources (e.g. geospatial socio demographics).
3. Information preparation
Construct modelling information by aggregating, manipulating and joining.
Morshona will integrate and manipulate your organisational data with own external data sources to create an integrated data set that is ready for analysis.
4. Modelling
Choose and apply various analytics modelling techniques.
During this phase Morshona apply sophisticated statistical techniques in order to discover and explain relevant relationships between safety outcomes and operational metrics. Combining traditional safety data with non-traditional sources some data can lead to predictions about where accidents are most likely to happen, under what circumstances, and to which segments of staff—all before they actually happen.
5. Evaluation
Evaluate analysis in the context of the business issues being addressed.
The model results are validated using statistical validation techniques. This phase typically involves a series of interactive workshops with the business to explore and contextualise the analytical findings. Moreover, the application of progressive cost optimisation modelling can help facilitate an objective assessment of the relative benefits of different safety spending options.
6. Deployment
Organise, present and deliver the insights in a way the organisation can use it.
The output from all previous phases is of little if not of any value if nothing is done with it. This phase covers the change management and best practices to build buy-in for predictive analytics to help bridge the gap between building analytical models and real world outcomes, including the monitoring requirements to drive proactive engagement across the organisation.
For more information on workplace health and safety, talk to our Morshona Advisory team
Comments